Plastic deep drawing
Technology
Technology
Deep drawing of plastics:
This is how our process works
In deep drawing, also known as thermoforming, a plastic sheet is initially heated until it can be formed. Then a vacuum is created with which the plastic is sucked into a temperature-controlled mould. The warm plastic sheet adapts to the mould contour and is then cooled to below the deformation limit by the temperature control of the mould and the blower, so that the plastic retains the final shape.
The result of the deep drawing process is precise and dimensionally stable. Not only the duration of cooling, but also that of heating depends on the thickness of the plastic sheets and the type of plastic.
What are the advantages of deep drawing plastics?
The deep drawing process of plastics is now a popular method for the production of individually shaped plastic components for various industries.
swissplast uses the innovative thermoforming process to quickly and efficiently produce high-quality plastic trays, moulded plastic parts and plastic transport containers. In addition to the cost factor of vacuum forming, the many possible materials are also positive aspects for thermoforming. The individualisation of plastic moulded parts is made particularly easy with vacuum thermoforming and vacuum deep drawing and has few limitations.
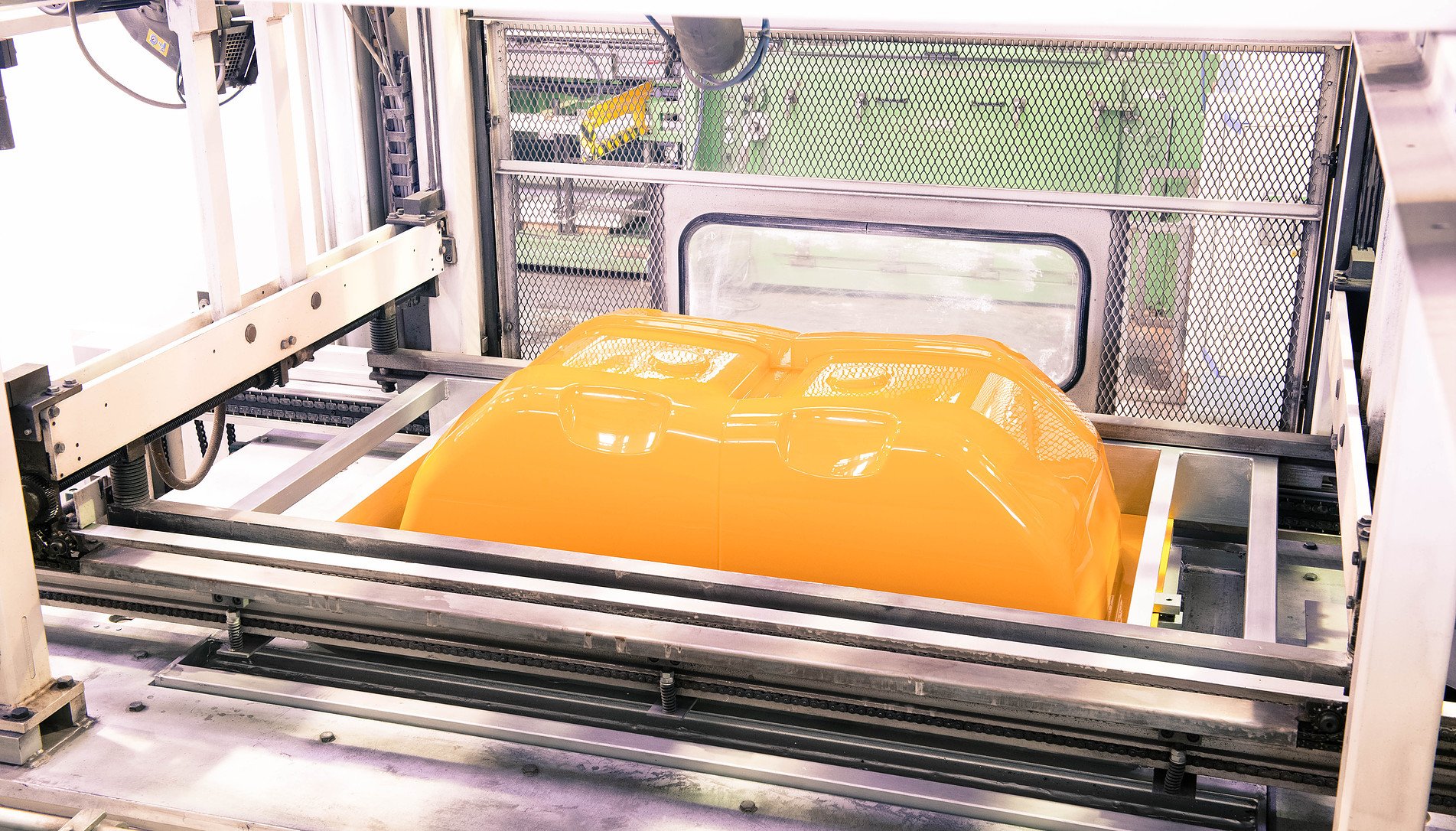
The benefits of deep drawing: price, weight & production time
Deep drawing is mostly used in the production of thin-walled plastic packaging such as disposable cups. The use of thermoforming is based on its numerous advantages. With thermoforming or deep drawing, for example, the production of smaller quantities is cheaper than with injection moulding or rotational moulding. This is due to the low tooling costs. Thermoforming also produces large batch sizes cost-effectively and quickly; a decisive advantage over GRP.
Another advantage is the low weight of the formed deep drawing parts. Since deep drawing produces thin-walled results, the parts are very light, which means that plastic packaging from swissplast saves costs in transport and logistics. In addition, the moulded, thin-walled plastic parts require little cooling time and are therefore fast in production.
Positive and negative forming
There are generally two approaches to the production of deep drawing parts.
The first method is positive moulding. Here, the dimensioning is done on the inside of the deep drawing part, and the moulding accuracy of the part is also on the inside. Ultimately, the shape is determined here by the moulding of the outer contour.
The second technique is the production of plastic parts by negative moulding. In this approach, the production of the part is done by moulding the inner contour. The dimensioning when drawing the moulded parts and their moulding accuracy is done here on the outside.
Plastics used for deep drawing
swissplast specialises in vacuum deep-drawing and is one of the world’s leading production facilities for plastic moulded parts in various industries. In principle, all common thermoplastics are suitable for the production of plastic parts:
PS (polystyrene)
ABS plastic (acrylonitrile-butadiene-styrene plastic)
PC (polycarbonate)
PMMA & PET (polymethyl methacrylate)
PE (polyethylene) & PP (polypropylene)
In addition, swissplast can further process the multilayer sheets (coextrusions) or material blends and regenerates made from the thermoplastics. There are also no limits to the surface finish of the plastic. swissplast produces a wide variety of surfaces and can work and manufacture to the highest quality standards, from high-gloss to very matt, from fine grained to leather grained, from printed to coated.
The process benefits of thermoforming in comparison:
The process benefits of thermoforming in comparison:
An overview of the advantages of deep drawing compared to GRP and injection moulding:
An overview of the advantages of deep drawing compared to GRP and injection moulding:
Price: In the price category, deep drawing compares very well. While GRP becomes financially unviable for long runs and injection moulding for short runs, deep drawing can offer an excellent price-performance ratio in all series sizes.
Weight: In the weight segment, thermoformed plastic parts are on a par with injection moulded parts. GRP cannot compete here, as the starting material is heavier. Deep-drawn moulded parts, however, have the advantage of comparatively high strength in addition to their low weight.
Dimensional accuracy: Another category in which deep-drawn parts stand out is manufacturing precision. Plastic moulded parts produced in the deep drawing process have a high fitting accuracy and easily match the production accuracy of GRP products.
Production time: Another major strength of plastic deep drawing is its unsurpassed production speed. While GRP and injection moulding can only produce slowly, especially for small series sizes, deep drawing consistently impresses with short production times.
Price: In the price category, deep drawing compares very well. While GRP becomes financially unviable for long runs and injection moulding for short runs, deep drawing can offer an excellent price-performance ratio in all series sizes.
Weight: In the weight segment, thermoformed plastic parts are on a par with injection moulded parts. GRP cannot compete here, as the starting material is heavier. Deep-drawn moulded parts, however, have the advantage of comparatively high strength in addition to their low weight.
Dimensional accuracy: Another category in which deep-drawn parts stand out is manufacturing precision. Plastic moulded parts produced in the deep drawing process have a high fitting accuracy and easily match the production accuracy of GRP products.
Production time: Another major strength of plastic deep drawing is its unsurpassed production speed. While GRP and injection moulding can only produce slowly, especially for small series sizes, deep drawing consistently impresses with short production times.
swissplast as the first choice for all aspects of plastic deep drawing
swissplast is one of the largest deep drawing companies in Europe. We always pay attention to the high quality of our deep drawing parts and use the latest technologies in plastics technology. We only use technically sophisticated plastics with a moulding area of max. 3000 x 2000 x 1000 mm for thermoforming or deep drawing. In addition, we pay attention to sustainability in plastic deep drawing in order to conserve the earth’s resources.
Do you have any questions about deep drawing or would you like some advice? Then please contact us.
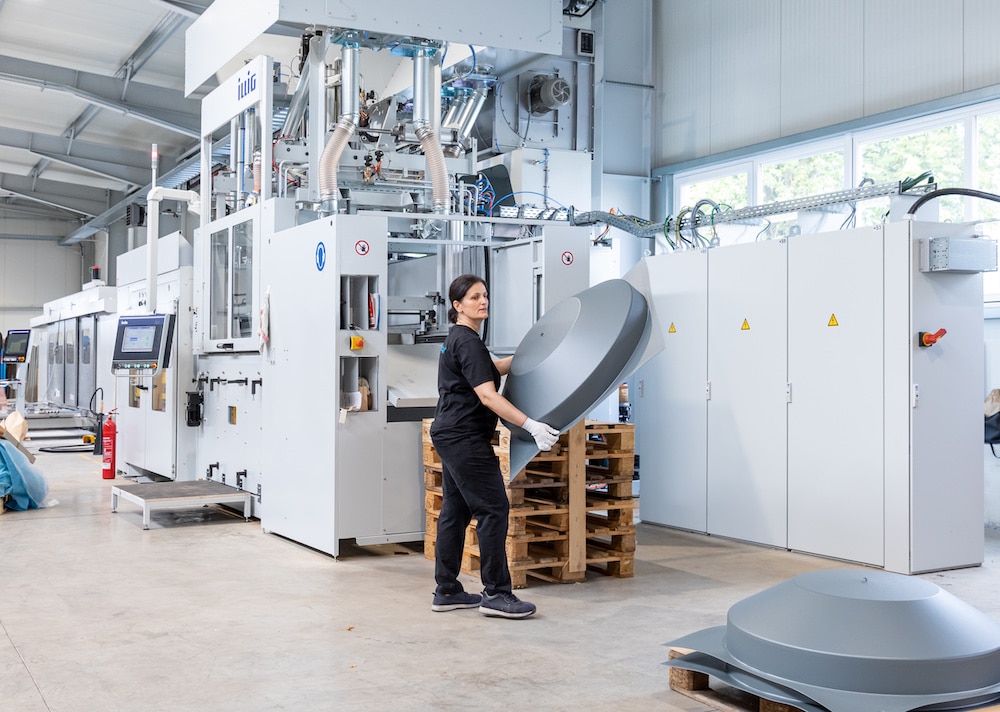
How does plastic deep drawing work?
Plastic deep drawing involves several work steps. We have summarised them briefly:
- Heating the plastic sheet: the plastic is heated until it becomes viscous and deformable.
- Deformation of the plastic: the sheet is preformed, increasing its surface area.
- Moulding of the plastic: the mouldable sheet is pulled over the stencil and takes its shape.
- Cooling and hardening: the deformed plastic is cooled, whereby it becomes solid again and retains its new shape.
Plastic deep drawing at swissplast
As one of the world’s largest producers of plastic mouldings, swissplast specialises in deep drawing, also known as thermoforming or vacuum deep drawing. The plastic moulded parts produced by swissplast are used in a wide variety of industries. Plastic thermoforming at swissplast is carried out according to the following steps, which are listed in detail here:
- Heating up the plastic: the initial sheets are heated up to such an extent that they can be formed. This process takes a few minutes, depending on the type of plastic and material thickness. With increasing heating, the plastic sheet melts and comes into a viscous state.
- Deforming the plastic: The heated initial sheet is brought into the correct initial shape by pre-stretching. In this process, the soft plastic sheet is put over the stencil and thereby takes on its rough basic shape.
- Moulding of the plastic: This is followed by the refinement of the moulded part. Now the plastic is brought into its planned and final shape. This can be done either with a vacuum or with compressed air. All cavities are removed in this production step so that the plastic part now sits directly on the stencil.
- Cool the plastic and remove it from the mould: This is the final step in plastic deep drawing. Once the moulding is complete, the moulded part is cooled down again so that it does not deform any further and then removed from the stencil. Excess edges on the moulded part are now removed. Subsequently, the plastic part can be refined by further work steps such as milling or assembly manufacturing.
swissplast works with both the positive deep drawing and negative deep drawing methods. The two deep drawing methods differ in whether the plastic sheet is drawn over a positive stencil or pressed into a negative stencil. The production times for vacuum deep drawing depend on the nature of the starting material. In general, however, one can assume a working time of a few minutes for a single deep drawing process.
Fields of application for vacuum deep drawing parts
Plastic moulded parts produced with the help of vacuum thermoforming are used in various industries today. In principle, there is no limit to where deep drawing parts can be used. Plastic parts in the medical industry, for example, are particularly important because of their simple hygiene and the associated patient safety. In the automotive industry and for commercial vehicles, too, moulded plastic parts such as plastic exterior trim or plastic interior trim are manufactured and processed using the deep drawing process. Thermoforming is also increasingly used in plant construction and mechanical engineering. In addition to the industries mentioned, deep drawing parts are also used in the packaging industry, in logistics, production and storage.
Why thermoforming?
Thermoforming plastic enables us to meet your requirements with the highest precision and quality. By using different production methods in thermoforming, we can deep draw plastic with the greatest flexibility and exactly according to your requirements. Our main method is vacuum deep drawing, which includes the two subcategories positive deep drawing and negative deep drawing. Due to different approaches, there are hardly any limits for us in terms of shape, material or sheet thickness. The advantages of deep drawing compared to other plastic processing methods are, among other things, the low price, the high precision and the speed of the deep drawing process. If you have any further questions regarding deep drawing of plastic, please do not hesitate to contact our team.
Further areas of interest